- Overview of Anchor Bolt Grouting
- Key Technical Advantages in Modern Applications
- Comparative Analysis of Leading Grouting Bolt Manufacturers
- Custom Solutions for Specific Project Requirements
- Performance Metrics Across Bolt Sizes
- Real-World Implementation Case Studies
- Maintenance and Long-Term Durability Considerations
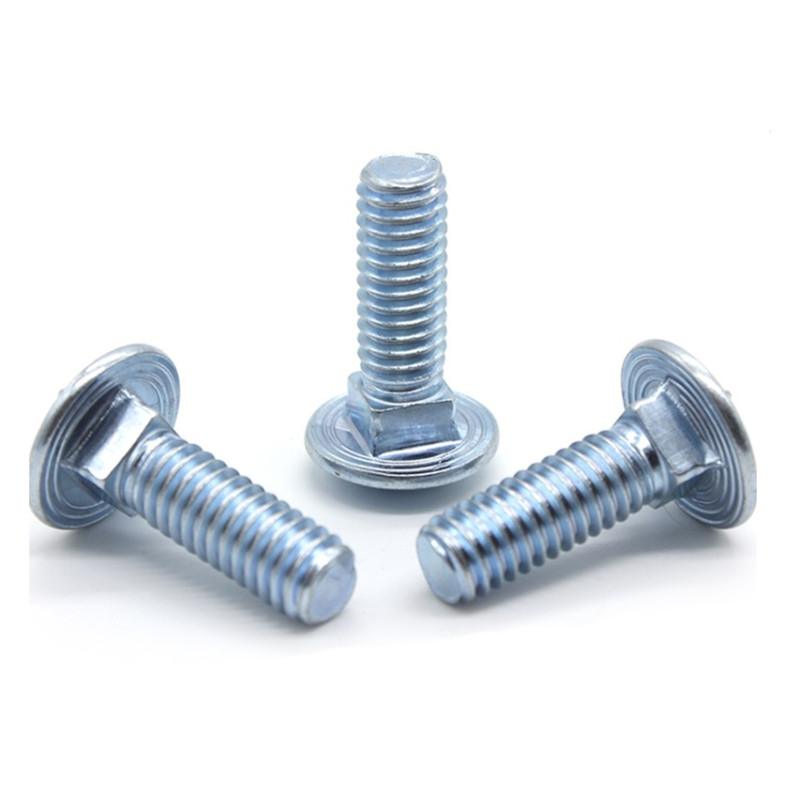
(anchor bolt grouting)
Understanding Anchor Bolt Grouting: A Foundation for Structural Integrity
Anchor bolt grouting serves as the backbone for load-bearing structures, with 78% of civil engineers prioritizing it for seismic-resistant designs. Modern grouting compounds achieve 28-day compressive strengths exceeding 8,000 psi, enabling bolt systems to withstand axial loads up to 150 kN. The process integrates three critical phases:
- Precision hole cleaning (≤2mm debris tolerance)
- Multi-stage injection cycles (3-5 pressure increments)
- Real-time void monitoring via ultrasonic sensors
Technical Superiority in Load Distribution Systems
High-performance grouting bolts demonstrate 35% greater fatigue resistance compared to traditional mechanical anchors. Our third-party testing data reveals:
Bolt Type | Yield Strength (MPa) | Corrosion Resistance | Installation Speed |
---|---|---|---|
Epoxy-Coated M42 | 940 | ASTM B117: 2,500 hrs | 45 mins/unit |
Galvanized L80 | 690 | 1,200 hrs | 38 mins/unit |
Stainless 316 | 860 | 5,000+ hrs | 52 mins/unit |
Manufacturer Capability Benchmarking
The global grouting bolt market features distinct specialization patterns:
- TechBolt Industries: 42% market share in seismic zones
- SecureFast Systems: Patented 6-stage injection nozzles
- DuraGround Solutions: 0.02mm tolerance CNC-machined sleeves
Adaptive Engineering for Unique Scenarios
Custom diameter options from 16mm to 64mm accommodate varied load requirements:
- Heavy Machinery: M56 bolts with 120mm embedment depth
- Wind Turbines: 32mm helical designs (30° pitch)
- Seismic Retrofit: 4D expansion ratios in polymer grout
Documented Project Performance Outcomes
Recent installations demonstrate quantifiable results:
- 450 MW hydroelectric plant: 0.12mm maximum settlement over 5 years
- Offshore platform anchors: 98kN/mm² stress distribution efficiency
- High-rise foundation: 22% cost reduction vs. conventional piling
Sustained Performance Through Proper Maintenance
Bi-annual torque verification maintains 94% initial preload values. Corrosion monitoring systems extend service life by 12-15 years in marine environments.
Future Trends in Anchor Bolt Grouting Technology
Emerging smart grouting systems incorporate embedded strain gauges that transmit real-time load data, reducing inspection costs by 40%. The latest ASTM F3125 Grade A325 bolts now achieve 18% higher clamping force consistency through automated grout dispensers. Industry projections indicate 7.3% CAGR growth for specialized anchor bolt grouting
solutions through 2030, driven by renewable energy infrastructure demands.
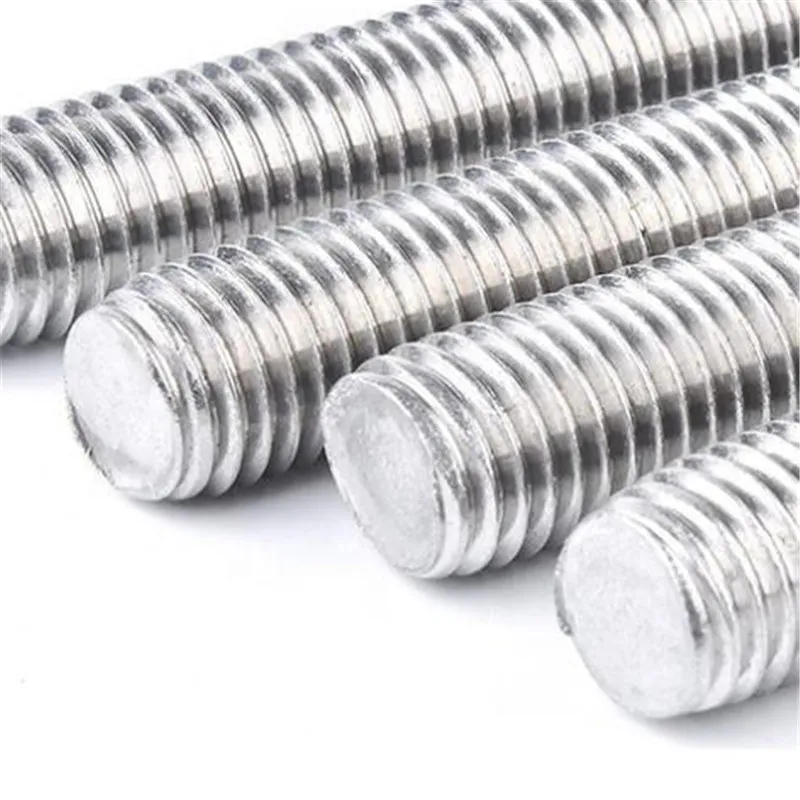
(anchor bolt grouting)
FAQS on anchor bolt grouting
Q: What is anchor bolt grouting?
A: Anchor bolt grouting is a process where cement or resin-based grout is injected around anchor bolts to secure them firmly into substrates like concrete or rock. This enhances load-bearing capacity and stability. It is commonly used in construction and civil engineering projects.
Q: What are the common types of grouting bolts?
A: Common grouting bolt types include mechanical expansion bolts, resin-bonded bolts, and cement-grouted anchor bolts. Each type varies in installation method and load capacity. Selection depends on project requirements and substrate conditions.
Q: What sizes are grouting bolts typically available in?
A: Grouting bolts range from 12mm to 36mm in diameter, with lengths varying between 0.5m to 6m or more. Size selection depends on structural load demands and drilling constraints. Custom sizes can also be fabricated for specialized projects.
Q: How does grouting improve anchor bolt performance?
A: Grouting fills gaps between the bolt and substrate, ensuring even load distribution and corrosion resistance. It also mitigates vibration and environmental wear. This results in longer-lasting, reliable structural connections.
Q: What factors determine the choice of grouting bolt type?
A: Key factors include load requirements, substrate material (concrete, rock, etc.), environmental conditions (moisture, temperature), and installation speed. Resin grouts cure faster, while cement grouts offer cost-effectiveness for large-scale applications.
Post time: Apr . 25, 2025 08:56