Drop in anchors have become an essential fastening solution in modern construction, mechanical, and industrial engineering applications. Renowned for their reliability and high performance, especially in concrete and masonry, these anchors are now available in various types, including 3/8 drop in anchors, 1/2 drop in anchors, 1/4 drop in anchors, and 3/4 drop in anchors. This comprehensive guide explores the latest industry trends, technical specifications, manufacturing processes, application cases, and product comparisons to help you make the best choice for your projects.
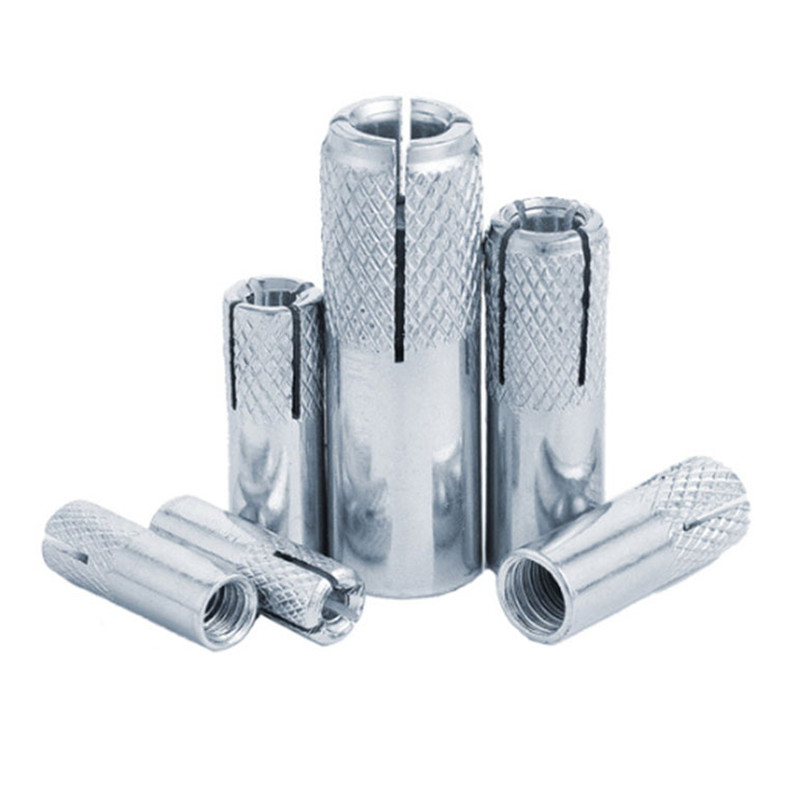
1. Overview and Industry Trends of Drop In Anchors
Drop in anchors are internal, female-threaded concrete fasteners designed for flush, permanent applications. Thanks to the expansion mechanism upon installation, they provide robust tensile and shear strength. In 2024, the global drop in anchors market is anticipated to exceed USD 780 million, with a CAGR of 5.3% through 2029 (Industry Report). Major growth drivers include:
- Rise in high-rise construction, industrial plant upgrades, and infrastructure expansion
- Increasing adoption in seismic-resistant and safety-critical applications
- Growing demand for corrosion-resistant and high-load fasteners
- Stringent standards such as ISO 898-2 and ANSI/SAE J429 boosting quality assurance
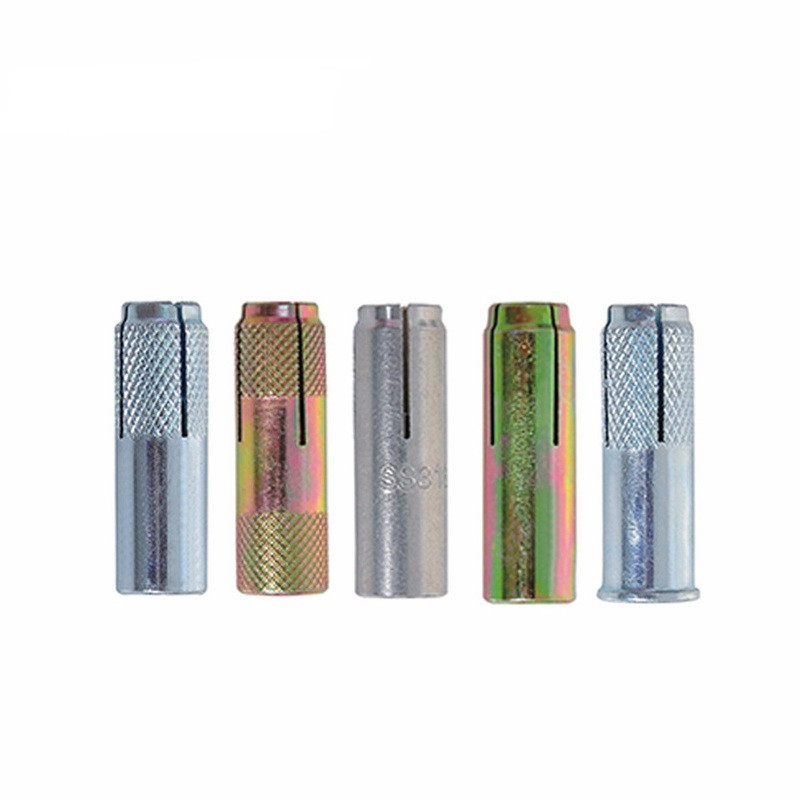
2. Technical Parameters & Product Specification Table
Explore a summary of standard sizes for drop in anchors and their respective design parameters:
Anchor Type | Thread Size | Anchor Length (mm) | Drill Hole Diameter (mm) | Min. Embedment (mm) | Allowable Tensile Load (kN) | Shear Load (kN) | Corrosion Resistance |
---|---|---|---|---|---|---|---|
3/8 drop in anchors | 3/8″-16 | 40 | 16 | 38 | 8.7 | 6.1 | Hot-dip Galvanized/SS |
1/2 drop in anchors | 1/2″-13 | 50 | 20 | 41 | 13.2 | 10.2 | Hot-dip Galvanized |
1/4 drop in anchors | 1/4″-20 | 32 | 10 | 25 | 4.6 | 3.8 | Electroplated Zinc/SS |
3/4 drop in anchors | 3/4″-10 | 70 | 28 | 67 | 25.8 | 18.1 | Hot-dip Galvanized/SS |
Drop in concrete anchors | — | Varies | Varies | Depends | Up to 30.0 | Up to 21.0 | PVC/SS/HDG |
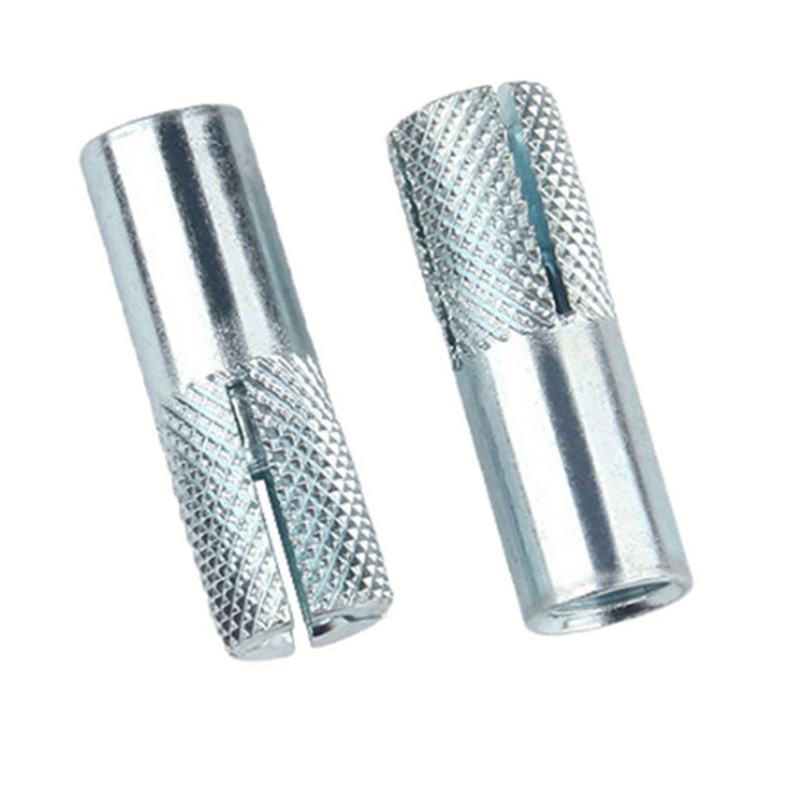
3. Production Process Illustration: Galvanized Carbon Steel Anchor
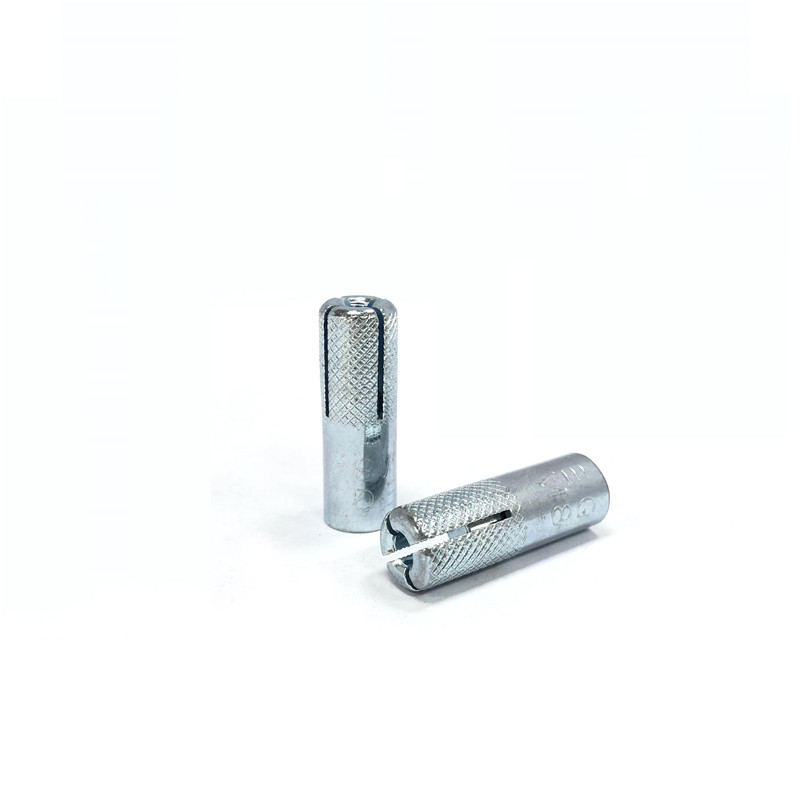
High-grade Q235/Q345 galvanized carbon steel is chosen for its strength, anti-corrosive properties, and compliance with ISO 898-2 & ASTM F1554.
Blanks are forged, followed by CNC turning to achieve ±0.02mm dimensional tolerance and perfect thread profile.
Zinc/Hot-dip galvanized (HDG) process per ISO 1461 for enhanced salt-spray test survivability (≥500hr).
Drop-in design integrates expansion cone. Quality checked at every interface using vision inspection systems.
Each batch is tested for tensile & shear in accordance with ANSI/SAE J429, and corrosion/fatigue as per DIN EN 1090-2.
Every anchor is laser-engraved with batch number. Export pack complies with RoHS/FDA and provides traceability.
View Product Details: Galvanized Carbon Steel Anchor
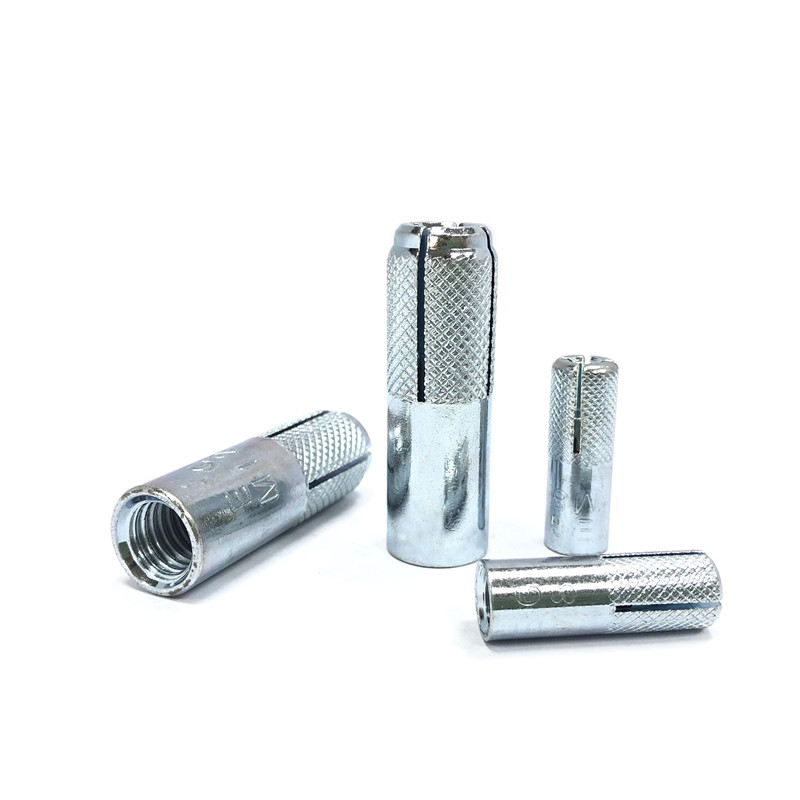
4. Competitive Comparison: Drop In Anchors Manufacturers & Customization
Selecting reliable drop in anchors suppliers is paramount. Below is a comparison of leading manufacturers, highlighting key technology and service parameters:
Feature | HBTBLS | Hilti | Powers | Simpson Strong-Tie |
---|---|---|---|---|
Core Material | Galvanized Carbon Steel (Q235/Q345) |
304/316 SS, Galv. Steel |
Carbon Steel, Zinc |
304 SS, Galv. Steel |
Certification | ISO 9001, CE, ANSI, RoHS |
ICC-ES, ISO |
UL, ISO |
ICC-ES, ISO |
Standard Sizes | 1/4″ to 3/4″ | 1/4″ to 1″ | 1/4″ to 1″ | 1/4″ to 1″ |
Factory Customization | YES (OEM/ODM, OEM stamping/marking) | NO | NO | NO |
Surface Coating | HDG, Electro-Galv. | HDG, SS | Zinc/HDG | HDG, SS |
MOQ | Small batches (500 pcs) |
>1000 | >500 | >500 |
Lead Time | 7~14 days | 21~30 days | 14~20 days | 14~20 days |
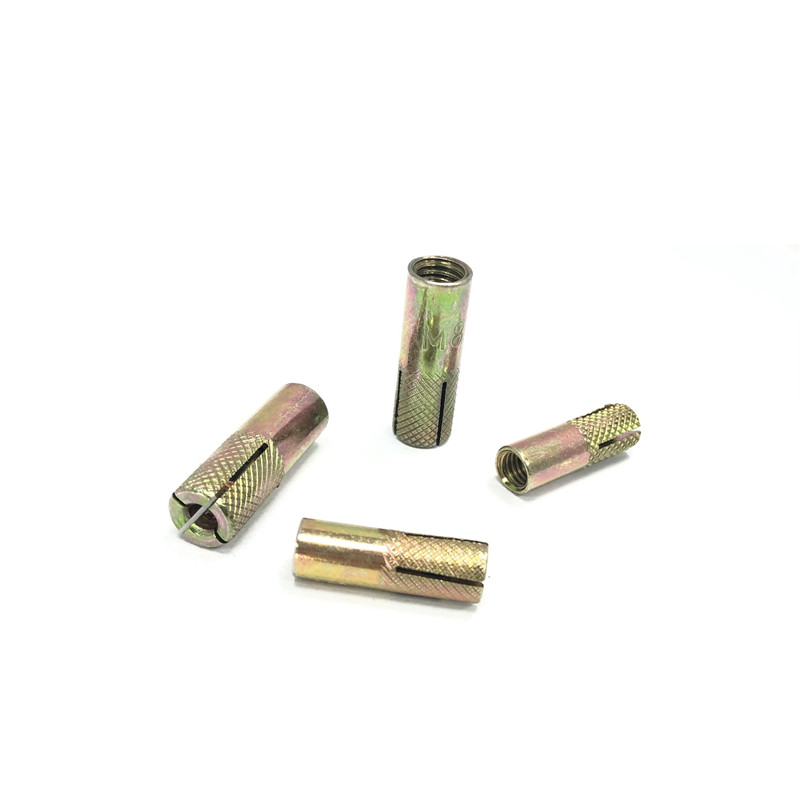
5. Custom Solutions: Applications & Case Sharing
5.1 Typical Application Scenarios
- Petrochemical Plants: For fixing heavy pipelines, pumps & cable trays. Advantage: anti-corrosive and fire resistant.
- Metallurgy/Steelworks: Anchoring support for machinery base in high-vibration, oily, or humid environments.
- Water Supply & Wastewater: Fastening of brackets and equipment to submerged or chemically active concrete structures.
- Bridges & Highways: Shear-resistant, high-load anchors for expansion joints, guardrails, seismic upgrades.
- Building Façade/Glass Curtain Walls: Flush install keeps surface aesthetics, critical for curtain wall suspension.
Case: Refinery Cable Tray Project — Middle East (2023)
- Client: Major EPC contractor
- Requirement: 20,000+ anchors (3/8″ and 1/2″), must withstand 96hr salt-spray, temp -10~60°C
- Solution: Custom drop in anchors using HDG carbon steel (Q345), batch traceable, 100% ISO 898-2 cert.
- Result: Zero anchor failure over 18 months, reduced labor by 24%
- Feedback: “Outstanding holding strength and anti-corrosion performance. On-site install efficiency increased by 30%.”
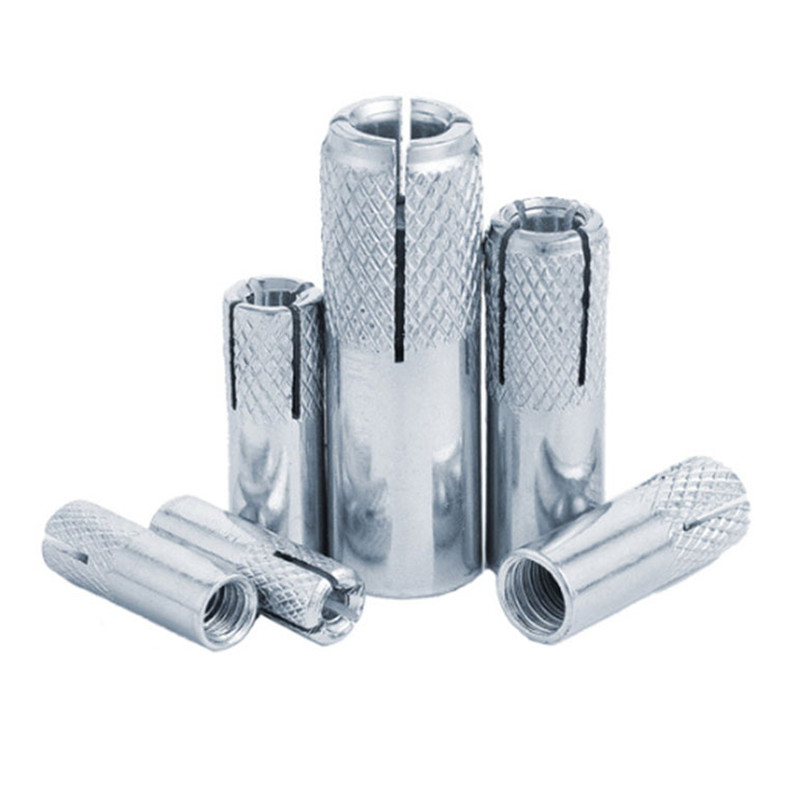
5.2 Performance Data Visualization
6. Why Choose Galvanized Carbon Steel Anchor?
- High Strength & Precise Tolerances: Load bearing up to 25 kN (3/4") under standard concrete compressive strength (fc = 30MPa).
- Superior Corrosion Protection: Hot-dip galvanized layer (min. 70µm) enables ≥500hr salt spray test. Fully compliant with ISO 1461, ensuring use in marine, chemical and humid environments.
- Global Certification: ISO 9001, CE, ANSI, RoHS, and batch-wise traceability for quality guarantee.
- Customizable Design: OEM logo, batch marking, length/thread customization (including M8~M24).
- Process Automation: Smart inspection ensures 99.8% batch pass rate.
- Eco-Friendly & Long-Lived: RoHS/FDA compliant, REACH safe. Service life of up to 18 years (inland) and 13 years (marine exposure).
- Comprehensive Customer Support: 24/7 pre-sales and after-sales technical support; site instruction available.
7. Professional Q&A: Drop In Anchors Terminology & Best Practices
8. Delivery, Certification & Support Guarantee
- Delivery: In-stock products ship within 3-7 days; custom orders generally within 14 days. Bulk/OEM supports expedited production.
- Quality Assurance: All drop in anchors batch certified (ISO, CE, ANSI, RoHS), full incoming/outgoing inspection per batch, batch traceability with unique QR code.
- Warranty: Standard 3 years for manufacturing/anti-corrosion. Extended warranty available.
- Customer Support: Free design consultation, sample testing, site technical guidance, and 24/7 troubleshooting.
Contact: sales@hbtbls.com (24h responsive)
9. References & Further Reading
Post time: Iyul . 28, 2025 06:01