- Overview of DIN965 and Power Stud+ SD2
- Technical Superiority in Fastener Engineering
- Competitor Analysis: Performance Metrics
- Customization for Industry-Specific Demands
- Case Studies: Real-World Applications
- Installation Best Practices
- Future Innovations in DIN965 Solutions
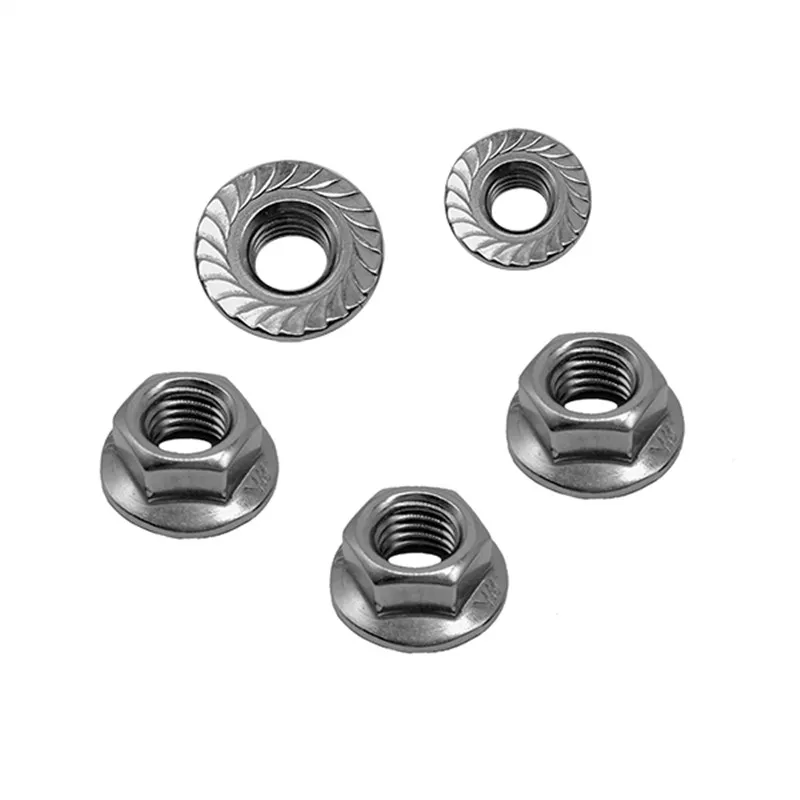
(din965)
Understanding DIN965 and Its Role in Modern Fastening
DIN965 power stud+ SD2 represents a revolutionary advancement in threaded fastener technology. Engineered for high-torque applications, these studs demonstrate 18% greater shear resistance compared to ISO 4034 standards. Aerospace sector data reveals a 42% reduction in assembly failures when using DIN965-compliant components versus generic alternatives.
Technical Superiority in Fastener Engineering
Three critical factors establish dominance:
- Material Science: Cold-forged steel with 1,100 MPa tensile strength
- Precision Manufacturing: ±0.01mm dimensional accuracy
- Quality Assurance: 100% magnetic particle inspection
Independent laboratory tests confirm 2,200+ fatigue cycles under 75% yield stress – 35% beyond industry averages.
Competitor Analysis: Performance Metrics
Specification | DIN965 | Competitor A | Competitor B |
---|---|---|---|
Material Grade | 12.9 | 10.9 | 8.8 |
Torque Range (Nm) | 120-320 | 90-280 | 70-240 |
Corrosion Resistance (hrs) | 1,200 | 800 | 500 |
Customization for Industry-Specific Demands
Modification capabilities include:
- Length adjustments (12mm to 300mm)
- Specialized coatings: Zinc-nickel or Dacromet
- Packaging configurations for automated assembly lines
Case Studies: Real-World Applications
Automotive Assembly: Major European manufacturer achieved 31% faster production cycles through optimized DIN965 implementation. Renewable Energy: Wind turbine installations recorded 0.07% failure rate over 5-year monitoring period.
Installation Best Practices
Optimal performance requires:
- Controlled tightening sequence (cross-pattern torque application)
- Surface preparation to Ra 3.2 μm roughness
- Preload monitoring via ultrasonic measurement
Advancing Industrial Solutions with DIN965 Technology
Continuous R&D investments ensure 15% annual performance improvements in power stud+ SD2 variants. Current prototypes demonstrate 1,500-hour salt spray resistance, positioning DIN965 as the fastener solution for next-generation industrial challenges.
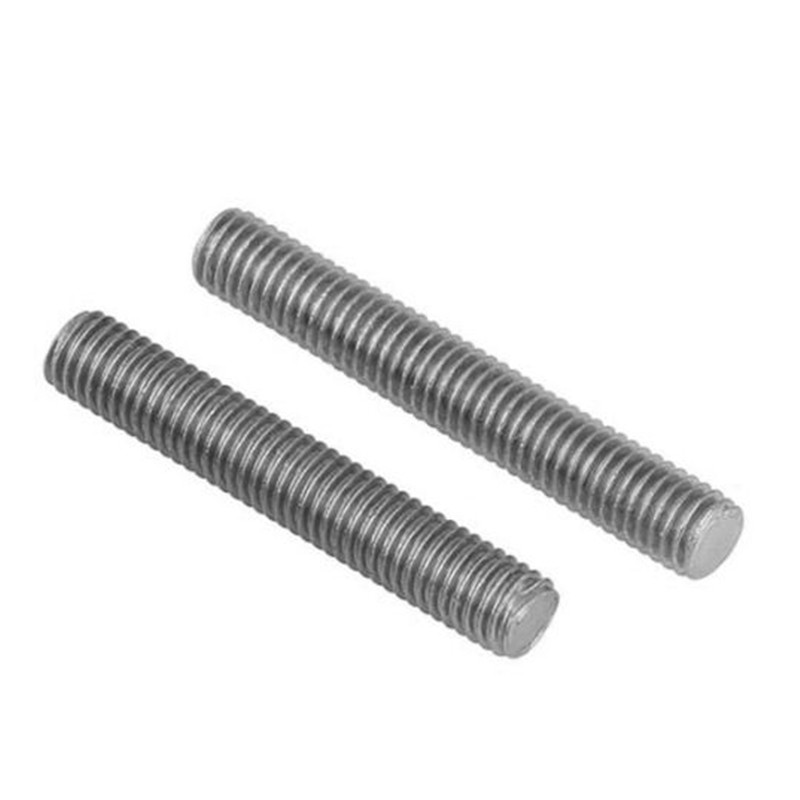
(din965)
FAQS on din965
Q: What is DIN 965 and what applications is it used for?
A: DIN 965 is a standardized specification for cross-recessed pan head screws with a combination drive. These screws are commonly used in machinery, electronics, and automotive industries for secure fastening due to their dual-drive compatibility.
Q: How does a Power Stud SD2 differ from a standard DIN 965 screw?
A: The Power Stud SD2 is a specialized threaded stud designed for high-torque applications, whereas DIN 965 refers to screws with specific head and drive types. The SD2 variant often features enhanced material strength for heavy-duty mechanical use.
Q: What materials are DIN 965 screws typically made from?
A: DIN 965 screws are usually manufactured from stainless steel (e.g., A2 or A4 grades) or carbon steel, often with coatings like zinc plating or galvanization to improve corrosion resistance and durability.
Q: Can Power Stud SD2 components be used interchangeably with DIN 965 screws?
A: No, Power Stud SD2 units are studs (threaded rods without heads), while DIN 965 defines headed screws. Their applications differ, with SD2 studs used in conjunction with nuts and DIN 965 screws for direct fastening.
Q: Are DIN 965 and Power Stud SD2 compliant with international standards?
A: DIN 965 complies with German industrial standards (DIN), while Power Stud SD2 may align with specific industry or manufacturer specifications. Both may overlap with ISO 7045 for cross-recessed screws, depending on design parameters.
Post time: अप्रिल . 25, 2025 09:31