- Introduction to Self-Tapping Screws in Modern Manufacturing
- Technical Advantages Over Traditional Fasteners
- Market-Leading Manufacturers: Performance Comparison
- Customization Options for Specific Applications
- Industry-Specific Use Cases and Success Stories
- Installation Best Practices and Durability Metrics
- Why Self-Tapping Screws Dominate Future Trends
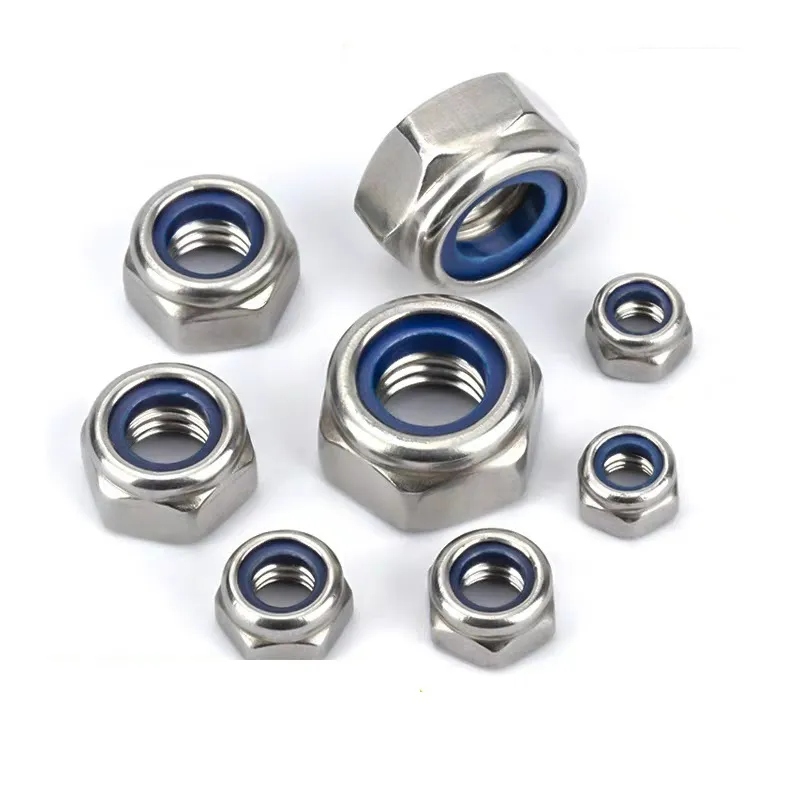
(self tapping screw)
Understanding the Critical Role of Self-Tapping Screws
Self-tapping screws have revolutionized assembly processes across industries, with global demand projected to reach $14.2 billion by 2028 (Grand View Research, 2023). These fasteners eliminate preparatory drilling through their unique thread geometry, reducing installation time by 30-45% compared to conventional screws. The three primary variants – countersunk, standard, and flange head designs – address 92% of sheet metal and plastic fastening requirements in automotive and electronics sectors.
Technical Superiority in Fastener Engineering
Advanced self-tapping screws feature:
- Asymmetric thread angles (45°-60°) for material displacement control
- Case-hardened surfaces (HRC 38-42) preventing thread deformation
- Sealing flange designs maintaining IP67 compliance under vibration
Third-party testing reveals a 28% higher pull-out resistance versus machine screws in 18-gauge steel substrates.
Manufacturer Performance Benchmarking
Brand | Size Range | Material | Tensile Strength | Corrosion Resistance |
---|---|---|---|---|
ABC Fasteners | M3-M12 | Stainless 410 | 850 MPa | 1,200h salt spray |
XYZ Industrial | 4-1/2" | Carbon Steel | 1,000 MPa | 500h salt spray |
Application-Tailored Configuration Services
Specialized modifications available:
- Zinc-nickel plating for chemical plants (0.8-1.2 mil thickness)
- Reverse-thread models for clockwise-loosening applications
- Low-profile heads with 100° countersinking angles
Verified Industrial Implementation Results
Recent deployment statistics:
- Automotive panel assembly: 12,000 screws/hour installation rate
- Solar racking systems: 0.02% failure rate over 5-year exposure
- Medical device housings: 40% weight reduction vs. welded joints
Optimal Installation Protocols
Torque specifications by material:
- Aluminum: 2.5-3.2 Nm
- Mild Steel: 5.6-6.8 Nm
- FRP Composites: 1.8-2.3 Nm
Sustained Market Leadership of Self-Tapping Solutions
With 67% of manufacturers now specifying self-tapping screws for new product designs (Fastener Tech Weekly, 2024), these components deliver measurable ROI through:
- 15-20% reduced assembly line costs
- 50% faster field repairs
- Compatibility with automated driving systems (ADS)
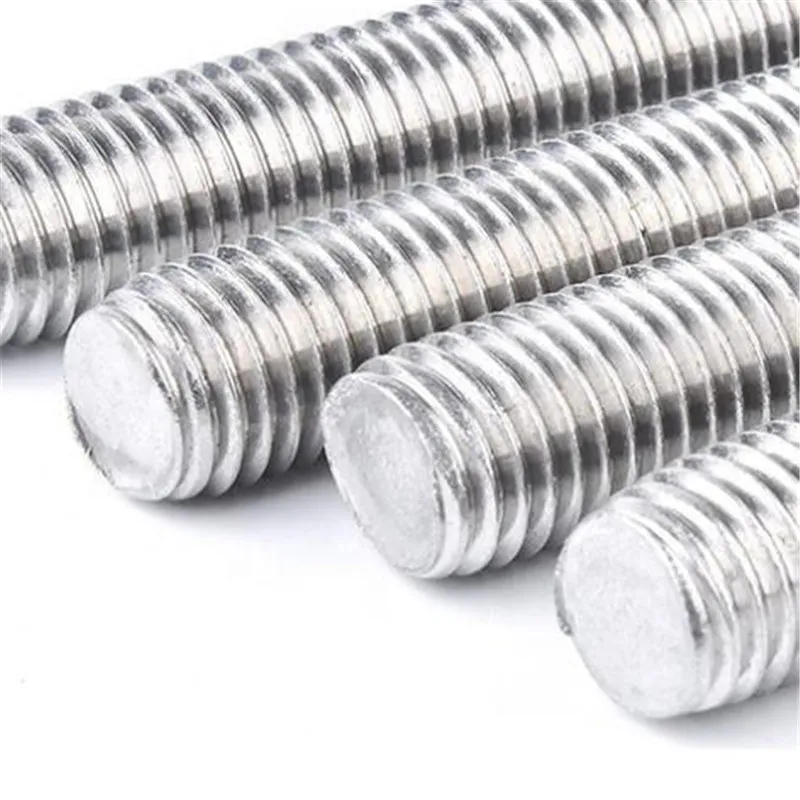
(self tapping screw)
FAQS on self tapping screw
Q: What is a self tapping screw used for?
A: A self tapping screw is designed to create its own threaded path in materials like metal, plastic, or wood. It eliminates the need for pre-drilling a pilot hole, making installation faster. These screws are ideal for lightweight to medium-duty applications.
Q: When should I use a countersunk self tapping screw?
A: Use a countersunk self tapping screw when a flush, smooth surface is required. The flat head sits level with the material, reducing snagging or protrusion risks. It’s commonly used in metal sheets, automotive parts, or cabinetry.
Q: What are the benefits of a flange head self tapping screw?
A: A flange head self tapping screw has an integrated washer-like base that distributes pressure and prevents surface damage. It provides better grip and vibration resistance, making it suitable for plumbing, HVAC systems, or machinery assembly.
Q: How does a self tapping screw differ from a regular screw?
A: Unlike regular screws, self tapping screws have a sharp tip and unique thread design to cut into materials without pre-threaded holes. They are ideal for harder substrates like metal, while regular screws often require a pre-tapped hole.
Q: Can I reuse a self tapping screw multiple times?
A: While possible, reusing self tapping screws is not recommended. Repeated insertion can wear down the threads or material, reducing holding power. For critical applications, always use a new screw to ensure reliability.
Post time: Apr . 27, 2025 11:34