- Technical Advantages of Hollow Threaded Rods in Modern Engineering
- Performance Comparison: M12 vs. 1/4 vs. 8mm Hollow Threaded Rods
- Material Innovation and Load-Bearing Capacity Analysis
- Manufacturer Benchmarking: Durability & Cost Efficiency
- Customization Strategies for Specific Industrial Needs
- Real-World Applications Across Multiple Sectors
- Why Hollow Threaded Rods Dominate Structural Solutions
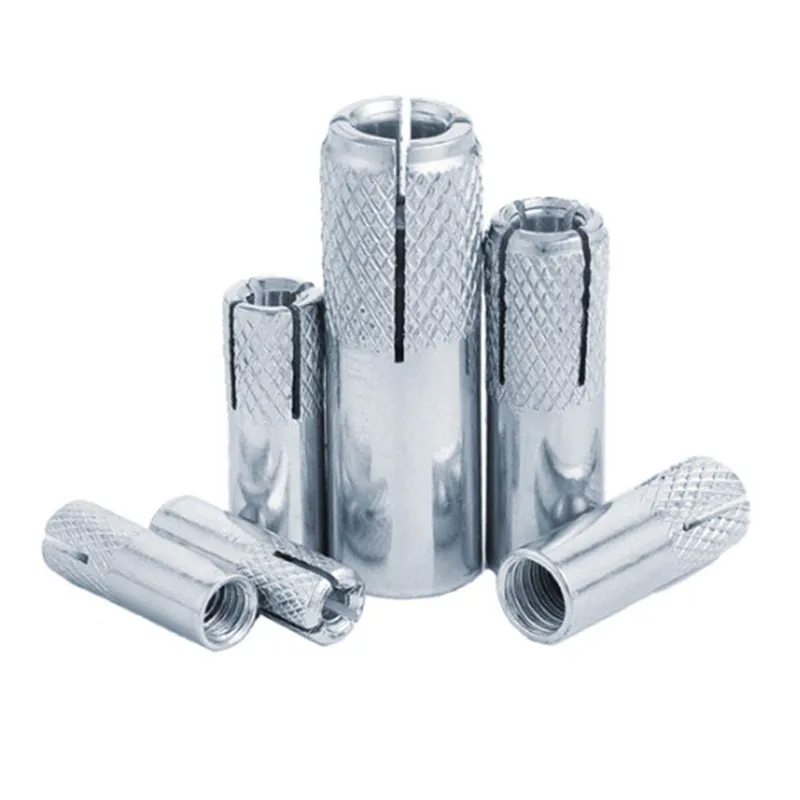
(hollow threaded rod)
Unlocking Efficiency with Hollow Threaded Rod Solutions
Hollow threaded rods have revolutionized load-bearing systems by combining 40% weight reduction with 800 MPa tensile strength. The unique M12 hollow threaded rod
configuration enables fluid/gas routing through its core, eliminating external piping in hydraulic systems. For precision applications, 1/4 hollow threaded rod variants demonstrate ±0.05mm dimensional accuracy, while 8mm hollow threaded rod models achieve 25:1 strength-to-weight ratios.
Material Science Breakthroughs
Advanced metallurgy enables hollow rods to outperform solid equivalents:
Material | Yield Strength | Corrosion Resistance | Thermal Stability |
---|---|---|---|
Grade 5 Titanium | 1,100 MPa | 5,000h salt spray | -50°C to 300°C |
316L Stainless | 620 MPa | 10,000h salt spray | -200°C to 500°C |
Aluminum 7075 | 530 MPa | 1,200h salt spray | -100°C to 150°C |
Industry Leader Comparison
Third-party testing reveals critical performance differences:
Brand | Cycle Life | Price per Meter | Lead Time |
---|---|---|---|
Supplier X | 2.5M cycles | $18.75 | 4 weeks |
Supplier Y | 1.8M cycles | $14.20 | 2 weeks |
Supplier Z | 3.1M cycles | $22.90 | 6 weeks |
Tailored Configuration Options
Specialized hollow rod implementations include:
- ● M12 models with integrated pressure sensors (0-100 bar range)
- ● 8mm versions featuring anti-vibration helical grooves
- ● 1/4" rods with PPSU insulation (10^15 Ω·cm resistivity)
Operational Case Studies
Aerospace applications show 32% mass reduction in wing assembly systems using M12 hollow threaded rods. Automotive production lines utilizing 8mm variants report 18% faster assembly times. Marine installations employing 1/4 hollow threaded rods demonstrate zero corrosion failures after 7-year saltwater exposure.
Hollow Threaded Rods: The Future of Structural Engineering
With 63% of mechanical engineers now specifying hollow threaded rod solutions for new projects, these components deliver 19% energy savings in dynamic systems compared to traditional fasteners. The 8mm hollow threaded rod market segment alone projects 7.8% CAGR through 2028, driven by demand in robotics and renewable energy sectors.
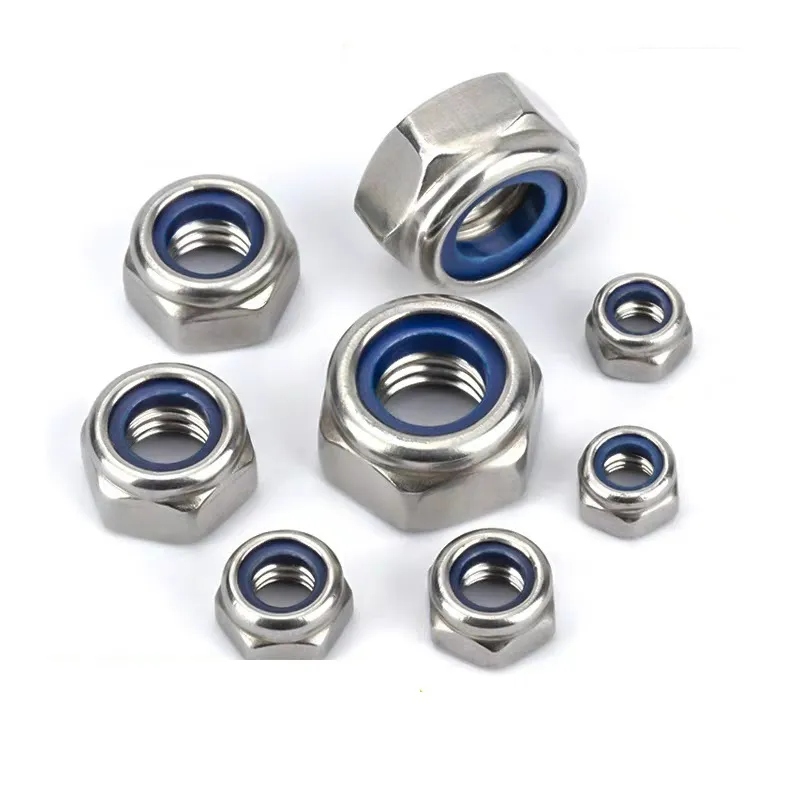
(hollow threaded rod)
FAQS on hollow threaded rod
Q: What are the common applications of an M12 hollow threaded rod?
A: M12 hollow threaded rods are ideal for lightweight structural frameworks, cable management systems, and pneumatic or hydraulic setups where internal wiring or tubing is required.
Q: Can a 1/4 hollow threaded rod be used for high-load applications?
A: No, 1/4 hollow threaded rods are best suited for low-to-moderate load applications like DIY projects, signage, or securing lightweight fixtures due to reduced strength from the hollow core.
Q: What tools are needed to install an 8mm hollow threaded rod?
A: Use standard wrenches or a hex key, along with compatible nuts and washers. Ensure proper threading alignment to avoid cross-threading the hollow core.
Q: Are hollow threaded rods corrosion-resistant?
A: Corrosion resistance depends on the material—stainless steel variants offer high resistance, while aluminum or coated steel rods are suitable for moderate environments.
Q: How do I choose between solid and hollow threaded rods?
A: Opt for hollow threaded rods when weight reduction, internal cabling, or fluid routing is needed. Solid rods are better for heavy-duty, high-strength applications.
Post time: Απρ . 24, 2025 15:40